4 min read
Preparations for Next Moonwalk Simulations Underway (and Underwater)
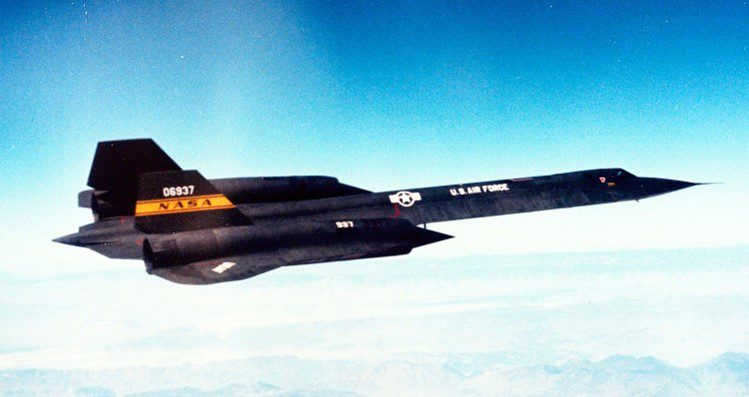
Supersonic flight became a reality in October 1947, when the Bell X-1 rocket plane broke the sound barrier. NASA’s Lewis Research Center in Cleveland (now, NASA Glenn), which had served as the agency’s aeropropulsion leader since it was established in the 1940s, subsequently helped NASA advance the technology needed to make longer supersonic flights possible.
A host of military aircraft capable of reaching supersonic speeds followed the Bell X-1. In the 1960s, Lockheed’s family of Blackbirds (the original A-12, the YF-12 interceptor, and the SR-71 reconnaissance vehicle) became the world’s first aircraft able to cruise at supersonic speeds for extended periods. However, the expansion of this capability to larger transport aircraft was difficult, in large part due to the lack of data collected about propulsion systems during longer supersonic flights.
To solve problems that weren’t found during design-phase testing of these aircraft and to advance crucial technology, like the supersonic mixed-compression inlet , the military loaned two retired YF-12s to the Dryden Flight Research Center (today, NASA Armstrong) in 1969 as part of a collaborative NASA/Air Force effort. They planned to compare data from YF-12 flights to data collected in wind tunnels at NASA’s Ames, Langley, and Lewis Research Centers.
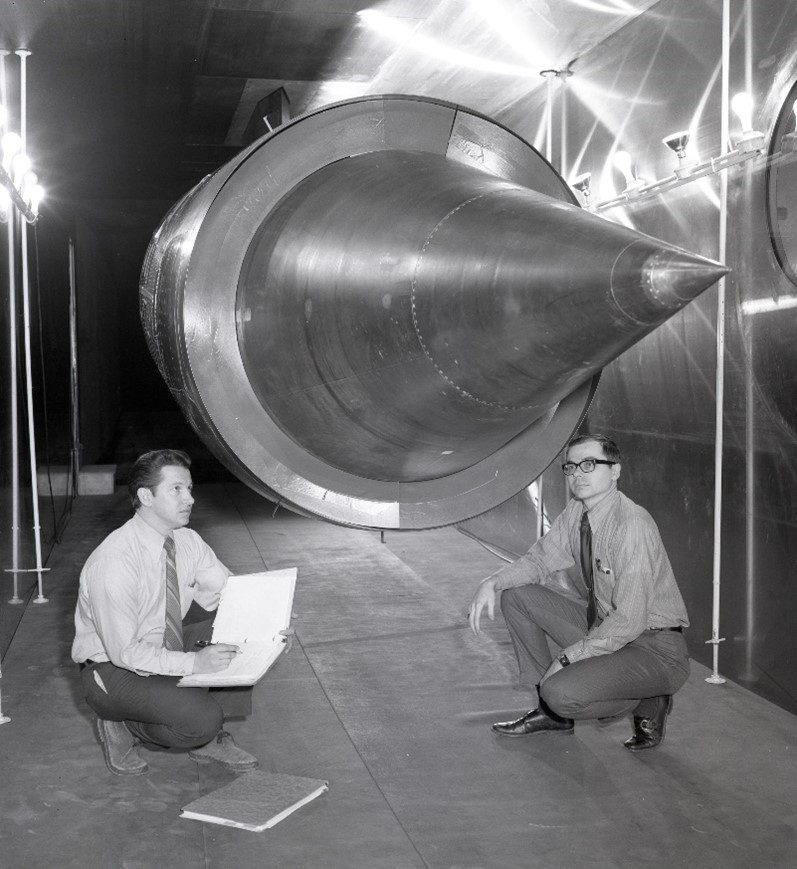
Lewis’ researchers had studied supersonic inlets in wind tunnels since the early 1950s and were in the midst of an extensive evaluation of supersonic nozzles and inlets using an F-106 Delta Dart . In this new effort, Lewis was responsible for testing a full-scale YF-12 inlet in the center’s 10×10 Supersonic Wind Tunnel and analyzing a 32,500-pound thrust Pratt & Whitney J58 engine in the Propulsion Systems Laboratory (PSL).
Although mixed-compression inlets, which allowed the engines to operate as turbojets at subsonic speeds and as ramjets at higher Mach numbers, were highly efficient, their design left the engines vulnerable to flow disturbances that often caused “unstarts.” Unstarts produced instantaneous drag that could stall the engine or cause the aircraft to quickly roll or yaw. Lewis researchers tested an actual inlet from a crashed SR-71, which they installed into the 10×10 in November 1971.
Over the next year, researchers collected aerodynamic data under different conditions in the wind tunnel. They also tested a new inlet control system patented by Lewis engineers Bobby Sanders and Glenn Mitchell that used mechanical valves to protect the aircraft against unstarts. It was the first time the system was tested on a full-scale piece of hardware.
Researchers also studied the relationships between the airframe, inlet, engine, and control system during normal flight conditions and when experiencing realistic flow disturbances.
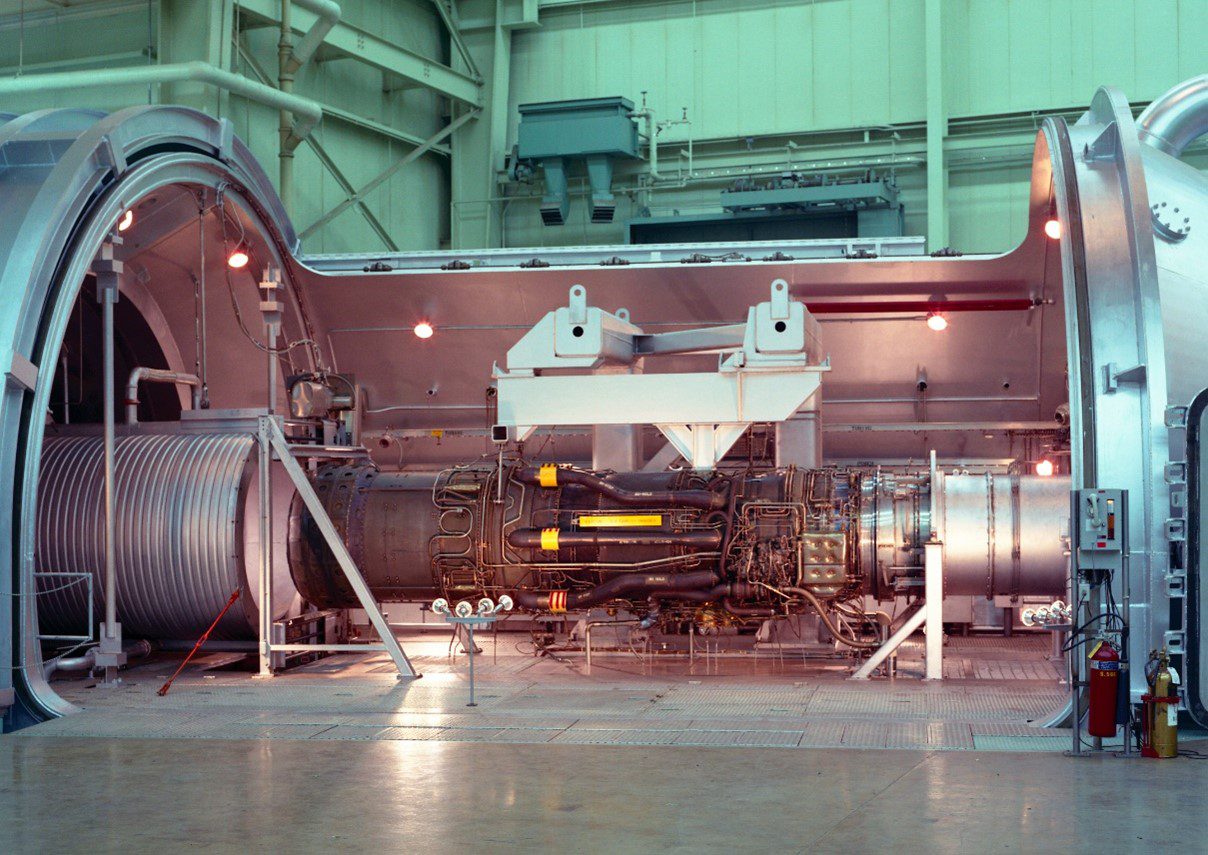
In the summer of 1973, a full-scale J-58 engine became the first hardware tested in Lewis’ new PSL second altitude chamber . For the next year, researchers captured data under normal conditions and while using mesh inlet screens to simulate in-flight air-flow distortions.
The PSL tests also measured the engine’s emissions as part of a larger effort to determine the high-altitude emissions levels of potential supersonic transports.
While the YF-12 program was terminated in 1979 as the agency’s aeronautical priorities shifted, a year’s worth of ground testing had already been completed in NASA’s wind tunnels and the YF-12s had completed nearly 300 research flights. The program had expanded to include the development of high-temperature instrumentation, airframe pressure and flow mapping, thermal loads, and the inlet control system.
NASA engineers demonstrated that small-scale models could be successfully used to design full-scale supersonic inlets, while the flight data was used to better understand the effect of subscale models and tunnel interference on data. Perhaps most importantly, the program at Lewis led to a digital control system that improved the response of the supersonic inlet to flow disturbances, which nearly eliminated engine restarts.
Many of the program’s concepts were integrated into the SR-71’s design in the early 1980s and have contributed to NASA’s continuing efforts over the decades to achieve a supersonic transport aircraft.
Additional Resources:
NASA Facts: The Lockheed YF-12
Mach 3+ NASA/USAF YF-12 Flight Research, 1969-1979 by Peter Merlin
Comments are closed.